Recommended Industry and Workpiece
Coolant processing equipment Carbide mold parts PunchCoolant processing equipment Liquid crystal and semiconductor parts Electric parts and materials
Coolant processing equipment Carbide drills and tools Drills/Taps/End mills
Coolant processing equipment Automotives/Automotive parts/Motorcycle parts Honing/EDM/Lapping
Product characteristics
The amazing 1.7 times higher filtration efficiency than our standard model!
The amazing 1.7 times higher filtration efficiency than model K.(Grinding sludge 5 to 15 μm)
High performance for collecting sludge which is difficult to magnetize. (ex. Coolant for grinding carbide tools)
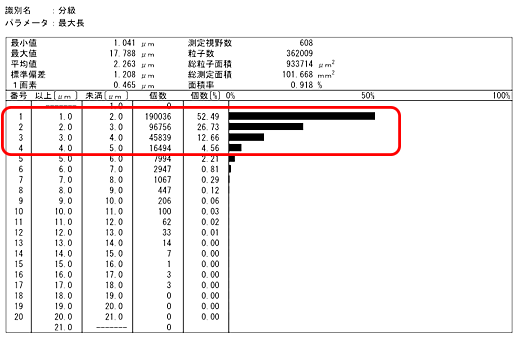
The volume of fine sludge less than 5 microns is more than 96%.
Repulsion magnetic circuit strengthen the magnetic power.
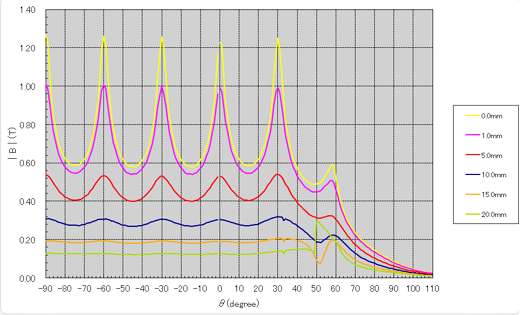
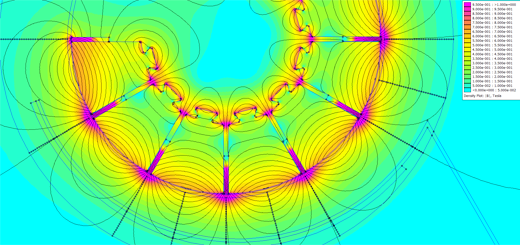
With the same basic structure as the magnetic separator for grinding machines, we have optimized the magnet arrangement in the drum.
And succeeded to increase its surface magnetic flux density to 0.9T.
Ideal for the device to collect fine magnetic sludge
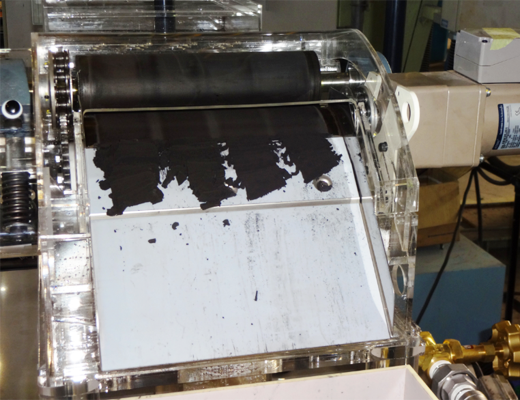
Magnetic sludge discharge condition
The UK FINE MAG can generate a high magnetic field, so it has great potential as a device for collecting fine magnetic metal powder.
In addition to the removal of the sludge which is generated from grinding process, it can be used as the recovery device of raw materials, or removal device of impure particles. FINE MAG has many other applications.
Improved productivity with continuous filtering
With the installation of UK FINE MAG, fine magnetic sludge can be collected continuously without suspending the production equipment.
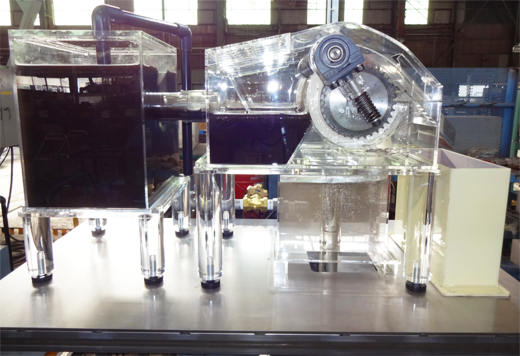
UK FINE MAG 【Left: Dirty coolant before filtering】 【Right: Clean liquid after filtering】
Improved squeezing efficiency
Coolant can be squeezed from the magnetic sludge attracted by the UK magnet drum using rubber rollers and discharged to the sludge box.
No consumables required
Almost no need of maintenance and extra costs because consumables such as filters are not required.
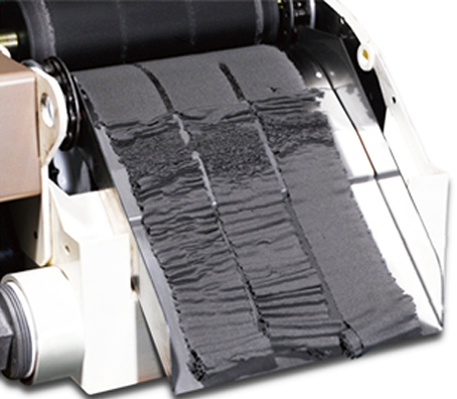
- Reduce the load of secondary filters such as paper filter, diatomite filter, and line filter, substantially.
- Excellent sludge collecting capability that helps to reduce significantly defects and the tank cleaning frequency. High squeezing performance ensures that the area around the machine is kept clean, contributing to the creation of a beautiful factory and better working environment.
- Sludge generated from grinding carbide tools and other materials that is hard to magnetize and fine sludge from honing or other processes can be collected.
- Increase the value of carbide sludge as a recyclable resource due to a high collection rate and squeezing performance. (ex. tungsten carbide)
Case Study
Case Study 1
- Test machine: FINE MAG UK-12
- Machine: Tool grinding machine
- Work: Carbide drill grinding (K model)
- Coolant: Water-soluble solution
- System: Offline (partial filtration)
- Period: March-April 2015
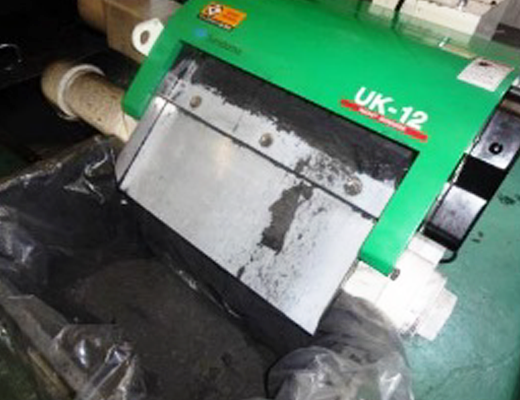
Test
The weight of each workpiece is measured before and after grinding. The number of pieces ground is also recorded and multiplied with the difference in weight before and after grinding to calculate the weight of the generated carbide sludge.
The collection rate is calculated by dividing the number with the carbide sludge weight collected using the UK model.
Result
Data on the weight of the carbide grinding sludge generated from groove cutting.
Result of monitoring the model UK from March 12 to April 17 | Total grinding weight (March 12 to April 17) | 6,769 g |
---|---|---|
Carbide sludge weight collected using the UK model (collected on April 20) | 3,553 g | |
Collection rate of FINE MAG UK | 52.5 % |
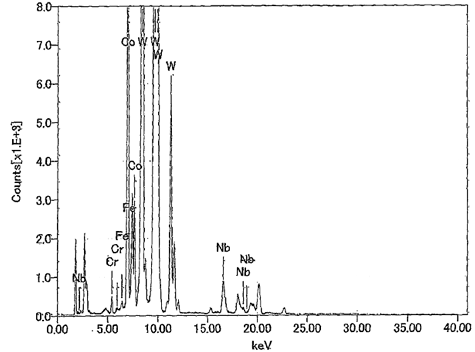
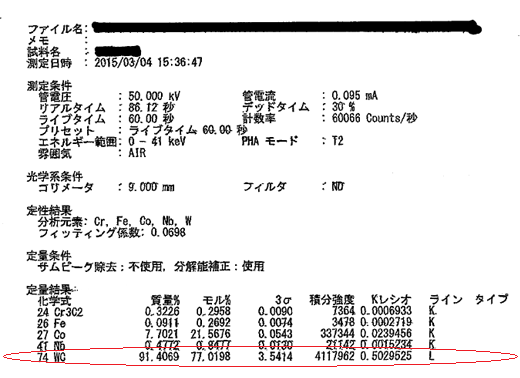
Result of analyzing the composition of the carbide sludge collected from the model UK: Approx. 91.4% tungsten carbide included.
Case Study 2
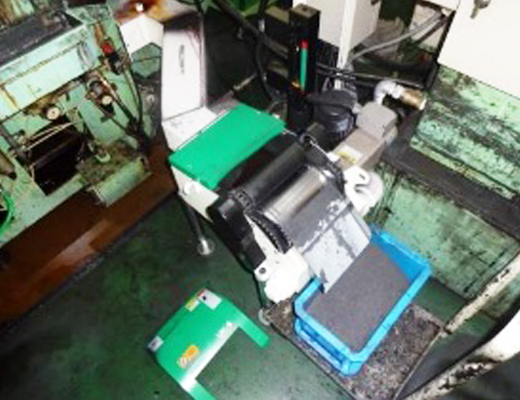
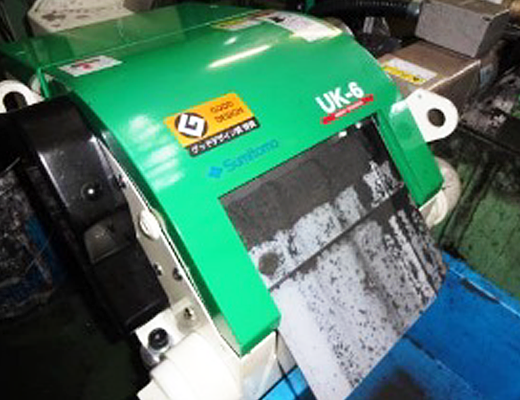
- Test machine: FINEMAG UK-6KY-1
- Machine: Groove grinding machine
- Work: Carbide tap (K and Z models)
- Coolant: Water-soluble coolant
- Processing volume: 60L/min
- System: Online
Result
Approx. 15 kg of carbide sludge is collected every month. If we assume the selling price to be 1,400 yen/kg, it will be 21,000 yen/month (15 kg/month x 1,400 yen).
Annually, it will be 252,000 yen (21,000 yen/month x 12 months).
In three years, it will be 756,000 yen (252,000 yen x 3 years).
Case Study 3
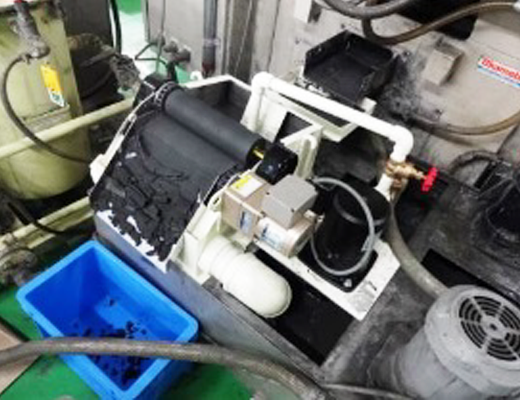
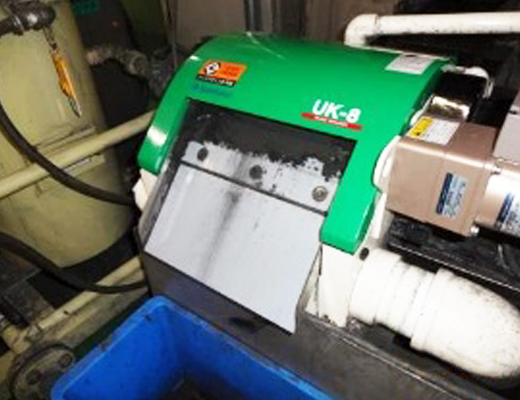
- Test machine: UK-8Y-1
- Machine: Rotary grinding machine
- Work: Carbide tap (K and Z models)
- Coolant: Water-soluble coolant
- Period: February-July 2015
Result
The average weight of the carbide sludge collected in three months is 49 kg/month. If we assume the selling price to be 1,200 yen/kg, it will be 58,800 yen/month (49 kg/month x 1,200 yen).
Annually, it will be 705,600 yen (58,800 yen/month x 12 months).
In three years, it will be 2,116,800 yen (705,600 yen x 3 years).
Case Study 4
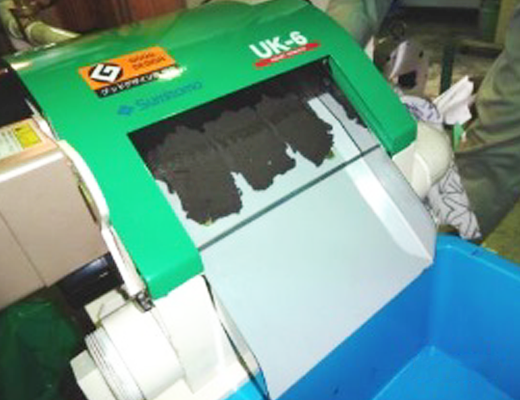
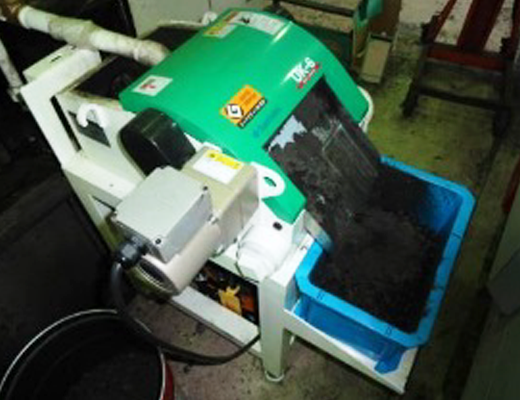
- Test machine: UK-6Y-1
- Machine: Electrical discharge machine
- Work: Mold (SKD)
- System: Offline (partial filtration)
- Period: February-September 2015
Result
Approx. 18 L (1 pail) of fine sludge is collected in two months from an electrical discharge machine.
The life of the secondary filter (2 μm) was extended from 300 hours to 400 hours. (before the model UK was installed)
The life of the secondary filter will extend further when the online flow system is adopted.
Product specifications
Specifications
Grinding machine | Cylindrical grinding machine (traverse grinding) |
---|---|
Processing volume | 60L/min |
Work | φ100×400 |
Feed rate | 10mm/s |
Analysis | Meets JIS B 9930 and JIS B 9931 standards |
Grinding wheel | N3A 80 J 8 VSK-1 |
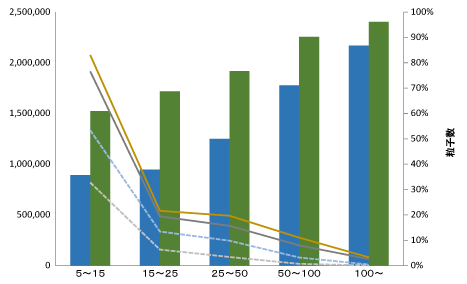
Grinding performance test result (counting method)
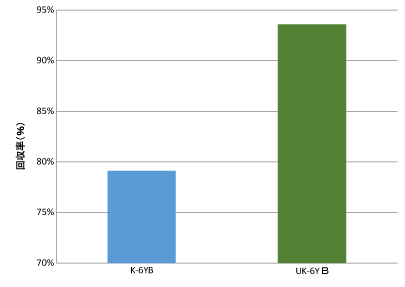
Grinding performance test result (weighing method)